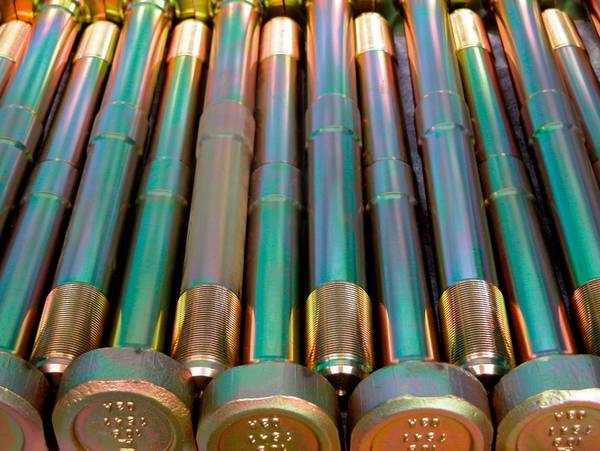
Hot drop forging
Hot drop forging means for mechanical part manufacturing
- 5 screw presses from 100 to 800 Tons.
- Induction heating: allowing a perfect mastering of forging parameters.
- Conduction heating: 1 electric mill stand able to upset up to 20 times initial diameter.
Productivity tools
- SMED – Single Minute Exchange of Die (Die tooling exchange in less than 10 minutes) to optimize our overall effectiveness
Capabilities
- Head Ø : 10 to 225 mm.
- Rod Ø : 8 to 110 mm.
- Length : until 1 m.
Hot drop forging advantages for special bolting and fastening parts
- Material savings
- Machining time reduction
- A thinner grain
- One-piece components.
- Improvement of mechanical properties.
Hot forging creates homogeneous and dense structure and metal fibre course is continued
Design
Tooling manufacturing (in carbide or special steels) is entirely integrated. Temperature checking systems ensure forging quality.
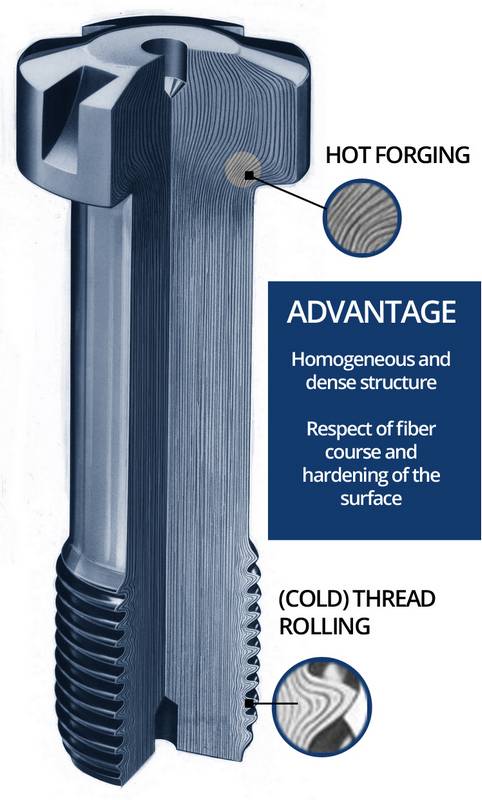